シミュレーションを活用した設備・機器の疲労評価
世の中に存在する鋼構造・機械の破損原因のうち、非常に大きな割合を疲労破壊が占めると言われています。その割合は、8割ともいわれています。
装置、機器類は何らかの動力によって稼働しています。そのため、動作時には必ず自身のアクチュエータ(エネルギーを回転などの物理的運動に変換する装置)による力や振動の影響を受けます。構造物も、風や波といった環境による力や、車両通過などの振動の影響で繰り返し応力が生じます。こうした繰り返し荷重によって生じる破断や亀裂などの疲労現象を疲労破壊あるいは疲労損傷と呼びます。
疲労破壊(疲労損傷)の評価、つまり「疲労評価」にシミュレーションを活用することで、労力の削減、工期短縮を図ることができます。
以下では、
- 疲労評価をシミュレーションで行う必要性
- 設備・構造物の疲労破壊事例
- 疲労評価の手法
について解説します。
なぜシミュレーションを活用した疲労評価が必要か
疲労評価は想定される繰り返し荷重を再現した実験的検討でも実施可能です。しかし、評価したい対象物によっては、規模が大きい、荷重の作用が複雑、などの理由で設備の準備など実験で再現することが難しい場合があります。また、実験することができたとしても、例えば設計検討において複数の設計案を試したい場合など、多くのケースを実験することは労力的、時間的にも難しい場合があります。
このような場合にシミュレーションを活用することで、実験設備や実験対象の準備が不要となるうえに、多くのパラメータスタディが可能となり、労力の削減、工期短縮を図ることができます。その際、評価対象の材質や強度、想定荷重の情報が多ければ多いほど、シミュレーションで用いるモデルの再現性が向上します。これにより、疲労評価の精度が向上します。
設備・構造物の疲労破壊事例
科学技術振興機構が立ち上げた「失敗知識データベース」※1には、航空機、自動車、鉄道車両、クレーンなど、長期間にわたり日常的に一定の同じ動きを繰り返す、あるいは振動している機器の疲労損傷事例が多く報告されています。
工場やプラントであれば、ボイラー、配管、ポンプ、回転機器などは常時稼働するので当然、疲労破壊・疲労寿命を考慮する必要があります。また、インフラ構造物でも疲労破壊を原因とする橋梁の崩落といった重大な事故が報告されています。
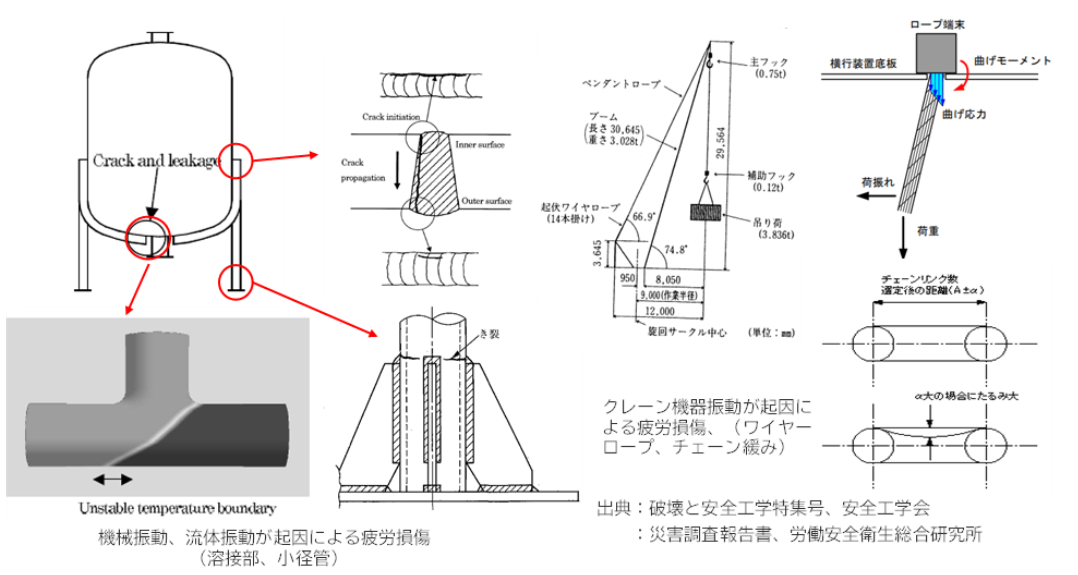
様々な疲労損傷例
破損例挿図出典元:
「石油・化学プラントの疲労損傷・事故の解析例」安全工学会 破壊と安全工学特集号Vol.32 No.6(1993)
「圧力設備の破損モードと応力(第4回)」圧力技術 講座 第43巻第4号(2005))
「天井クレーンの巻上用ワイヤーロープの破断災害」災害調査報告書 労働安全衛生総合研究所
※1 失敗知識データベース:2001年8月10日文部科学省発表の「失敗知識活用研究会報告書-失敗経験の積極的活用のために-」の中の提言のひとつ、「失敗経験から獲得された新たな知識・データ等を構造化したデータベースの構築」を受け、国立研究開発法人科学技術振興機構(JST)が推進、2005年3月に公開したものです。現在は特定非営利活動法人失敗学会において運営されています。
疲労破壊と評価方法
疲労破壊(疲労損傷)とは
疲労破壊(疲労損傷)とは、部材が繰り返し応力を受けることで、静的な強度(静強度)以下であっても損傷が進み、最終的に破壊に至る現象です。疲労破壊の現象は、主に応力集中部に生じる繰り返し応力(ひずみ)レベルと荷重作用サイクル数で決まってきます。
疲労評価のステップ
実構造物の疲労評価を行うには、大きく分けて、
- 実働荷重の評価
- 実構造物に発生する応力・ひずみの評価
- 評価方法の選択
- 材料データの選択
が必要となります。
それぞれのステップでは、選択すべき解析手法や、考慮すべき項目、その他、影響する項目に留意する必要があります。
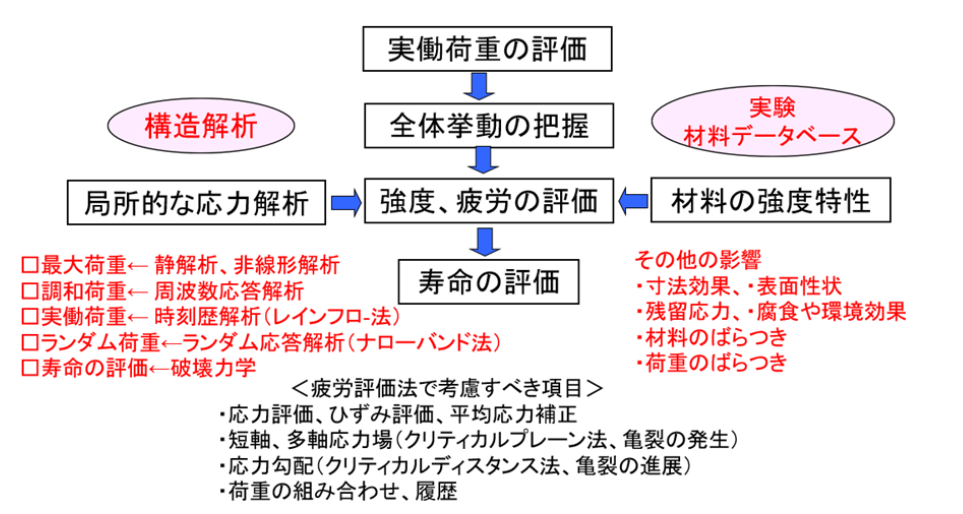
疲労評価の概要
疲労評価の方法
シミュレーションに基づく疲労評価には以下の方法が用いられます。
1.応力による評価法
応力による方法はStress-Life Approachと呼ばれ、材料のS-N線図(応力振幅と破断サイクル数の関係)と共に最もよく使われます。下図に荷重サイクルの定義、S-N線図の模式図を示します。図では、異なる3パターンの平均応力の場合のS-N線図を示しています(※平均応力の影響は後述するダウンロード資料内に記載しています)。
S-N線図は、破断サイクル数に応じて、低サイクル疲労、高サイクル疲労、超高サイクル疲労の大きく3つの領域に分けられます。高サイクル疲労では、おおよそN = 104~108の破断サイクル数となり、Stress-Life Approachが使われます。N = 108以上では、超高サイクル疲労となり、鉄鋼材において疲労限度以下では無限の寿命を持つことになります。高速回転体などの繰り返し曲げ疲労では疲労限度以下の応力振幅に設計する必要があります。
一方で、黄銅やアルミ合金など非鉄金属材では疲労限度が現れず107~108回を超えても線図は下がっていきますので注意が必要です。コンクリート系材料では、上記の様な領域の分け方はされず、106回程度までのS-N線図を取得して参照することが行われます。
![]() |
![]() |
繰り返し荷重の定義 |
材料のS-N線図 |
【評価応力値の算出】
試験片より実験的に求められたS-N線図と、実際の複雑かつ不連続な構造体で発生する応力を比較するためには、工夫が必要になります。実際の構造体では公称応力やホットスポット応力を算出してS-N線図と比較しています。
公称応力による疲労評価
局所的応力集中を考慮しない公称応力(軸応力+曲げ応力)と溶接継手タイプ毎のS-N線図を比較します。日本鋼構造協会や造船協会から実績のあるS-N線図が示されています。しかし、形状が複雑になるほど公称応力の定義が難しくなり、参照するS-N線図も近いものが当てはまらなくなります。この場合にホットスポット応力が用いられます。
ホットスポット応力(HSS)による疲労評価
複雑な3次元形状モデルでのFEM解析結果を用いて疲労評価する場合に使用します。応力集中部近傍の応力分布をある程度細かいメッシュで求め、応力集中部近傍の1点の応力値、または2点から外挿した応力値を評価点での応力振幅とします。この場合は、平滑母材のS-N線図を参照します。
※より詳しい情報はダウンロード資料に掲載しております。
2.ひずみによる評価法
先に説明した低サイクル疲労はN = 104回程度以下の繰り返し回数で疲労破壊する現象です。地震時や台風時、装置の起動停止時、ヒートサイクル時などに受ける比較的大きな荷重下で、破壊までに多くの塑性変形が含まれる延性破壊現象には、ひずみによる方法(Strain-Life Approach)が用いられます。大きな荷重が作用する場合、小さな荷重に比べて、評価対象の塑性化が進みます。この際、塑性ひずみ(元に戻らないひずみ)が生じるため、応力で評価するのは適切ではありません。従って、ひずみによる評価が有効です。
ひずみによる評価の場合、生じるひずみ振幅と破断までの繰り返し回数の関係をまとめたE-N線図(Manson-Coffinの式)が参照されます。ひずみ評価の場合、応力評価と異なり切り欠き係数やSCFを考慮する必要はなくなり、直接E-N線図と比較できますが、非線形弾塑性解析により全ひずみ(弾性ひずみ+塑性ひずみ)を算出する必要があります。
または、線形解析から塑性ひずみを算出する方法にNeuber則があります。線形解析で得た応力値から塑性ひずみを含む局所ひずみを疑似的に推定できます。一方、繰り返し応力―ひずみの関係は、Ramberg-Osgoodの式で近似的に表現できます。下図 に示すようにNeuber則の式とRamberg-Osgoodの式をプロットしたときの交点を推定ひずみ値として利用します。
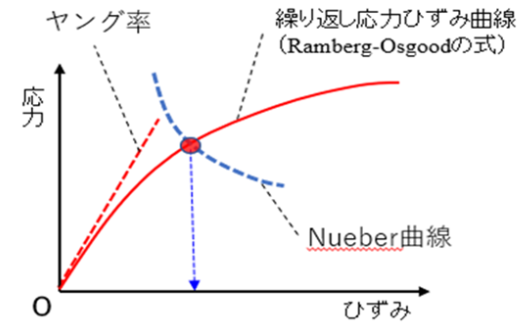
Neuber則を用いたひずみ推定
3.破壊力学による評価法
上記の応力またはひずみによる評価は、設計的には非常に有用ですが、基本的には想定した条件下で疲労破壊が生じるか生じないかの評価となります。
実際の破壊プロセスは、初期亀裂の発生(または初期亀裂の存在)→ 亀裂の進展 → 最終破断を辿ります。初期亀裂の存在を認め亀裂の進展による疲労破壊ではS-N線図やE-N線図では説明が困難であり、破壊力学による方法(Fracture Mechanics Approach)が必要となります。逆に破壊力学では、亀裂発生までの寿命は求められないので、亀裂が存在している状態からの余寿命を評価するか、極微小な亀裂が存在しているとして寿命評価をします。
破壊力学による評価法では、応力振幅の代わりに応力拡大係数範囲(ΔK)により亀裂進展速度(1サイクルあたりの亀裂進展量)を推定するParis則がよく用いられます。Paris則を積分することにより、構造物の寿命サイクルNfを見積もることができます。
下図は、ΔKと亀裂進展速度の関係をグラフ化したものです。ΔKがΔKth値以下であれば、亀裂進展速度は0であり進展しません。逆にΔKc値に近づくと急激に進展速度が増大し最終破断に至ります。
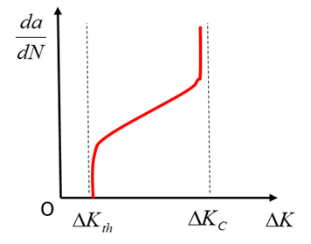
Paris則線図
実働荷重の定義とシミュレーション
実働荷重の定義
実働荷重とは、実際の使用条件下で構造部材に作用する荷重のことです。シミュレーションによる疲労評価の方法は、前項でお伝えしたとおり
- 応力による評価法
- ひずみによる評価法
- 破壊力学による評価法
が用意されています。
ですが、実際の構造物は、試験体とは異なり複雑な形状です。そのため、様々な方向から力がかかる「多軸応力」状態であったり、外部からの力が一定期間残ってしまう「残留応力」も存在します。また、作用する荷重履歴も複雑となり、正確な応力値やひずみ値の算出、および、荷重サイクル数を見積ることは一般に難しい作業になります。シミュレーションを行う場合には、対象となる構造物や機器の状況に応じて、手法を使い分ける必要があります。
シミュレーションの手法
評価対象である設備や機器の状態や使用環境などに応じて、下記のさまざまな手法の中から適切なものを選択します。
静解析・非線形解析 (一定繰り返し荷重時) | ・想定荷重下での疲労評価部位の応力・ひずみを算出します。繰り返し荷重は一定に繰り返すとして、応力評価またはひずみ評価を行います。または残留応力、死荷重での応力を算出し平均応力の評価に使用します。 |
周波数応答解析 (複数レベルの繰り返し荷重時) | ・共振時を含む疲労評価部位の応力・ひずみを算出します。いくつかの周波数での応答値をグルーピングしマイナー則により累積損傷率を評価します。 |
時刻歴応答解析 (非定常、非比例の荷重時) | ・時間変化する疲労評価部位の応力・ひずみを算出します。レインフロー法を用いて時刻歴荷重レベルをブロック分けし、マイナー則により累積損傷率を評価します。 |
ランダム周波数応答解析 (風荷重、常時振動、搬送時振動などランダム荷重時) | ・統計的な発生応力値を使用します。パワースペクトル密度(PSD)のカウント法であるナローバンド法などを用いて累積損傷率を評価します。 |
回転翼固定リベット部の疲労強度評価|事例
回転翼固定リベット部について、疲労評価をおこなった事例をご紹介します。
まずFEMモデル化し、翼の回転速度に対する遠心力を外力とする静的な応力解析を実施して、その最大主応力を平均応力値とします。
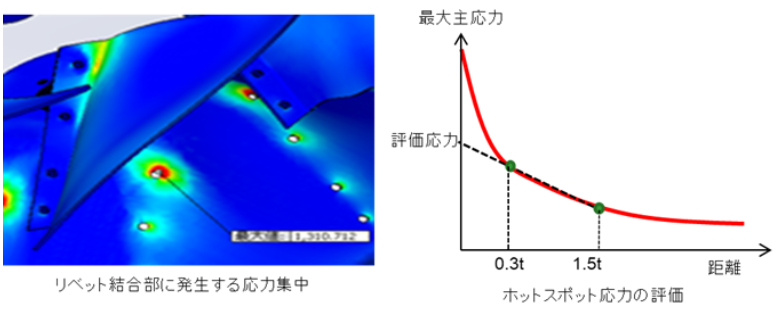
FEM解析結果とホットスポット応力の算出
続いて、回転不釣り合い力による周波数応答解析を実施し、1次、2次共振時の繰り返し最大最小主応力を応力振幅値とします。それぞれ算出した平均応力と応力振幅を疲労限度線図にプロットしました。いずれの点も降伏限界と修正グッドマン線図の内側に収まっており、想定される稼働状況では疲労損傷しないと言えます。
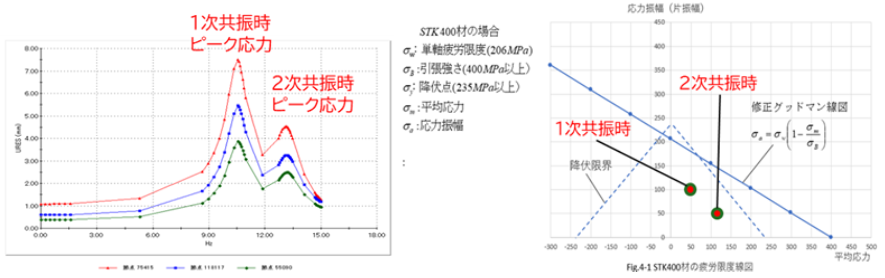
周波数応答解析の結果と疲労限度線図
損傷度は疲労損傷が生じるサイクル数に対する、発生するサイクル数の割合として定義されます。
この事例においては、発生サイクル数は共振周波数と想定する稼働時間から算出できます。また、損傷サイクル数は疲労限度線図より求められます。
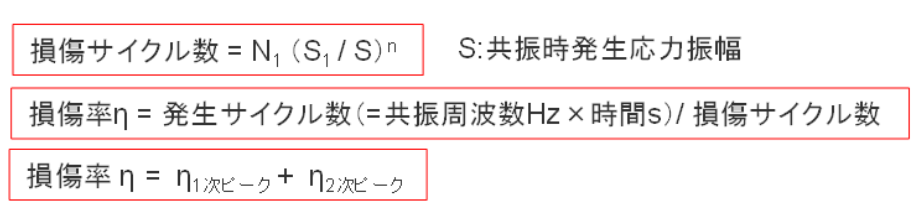
疲労評価 解析コンサルティング サービスの概要
対象の構造物・設備の「規模が大きい」「荷重の作用が複雑」などの理由で実験が難しい場合や、設計検討において多くのケースを実験したい場合にシミュレーションを活用することで、実験設備や実験対象の準備が不要となるうえに、多くのパラメータスタディが可能となり、労力の削減、工期短縮を図ることができます。
構造計画研究所では
- 振動解析を用いて設備・構造物の疲労現象を定量的に評価します
- 対象設備の使用環境や振動原因などに応じて最適なモデル化や解析手法を選定し、精度の高い疲労評価を行います
疲労評価を行う際には、実働荷重の評価、実構造物に発生する応力・ひずみの評価、評価方法の選択、材料データの選択をノウハウに基づき適切にご提案します。
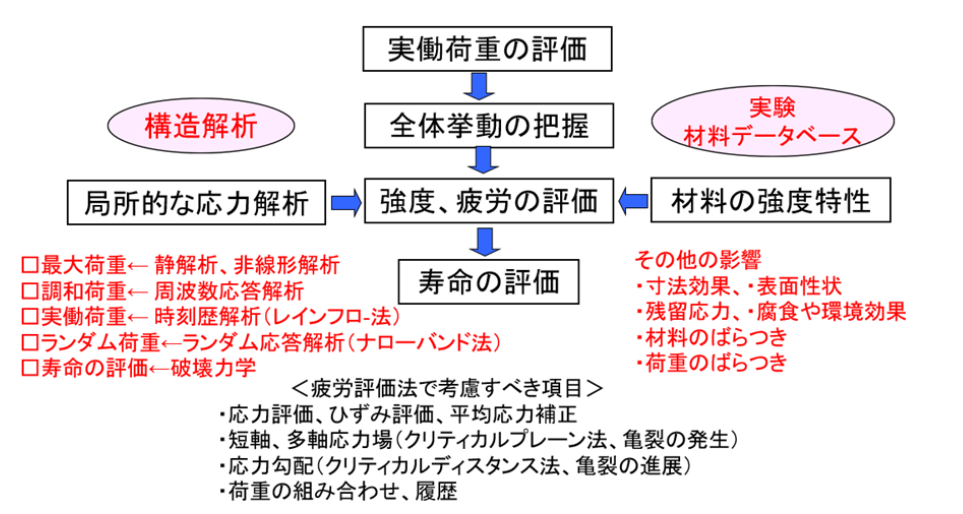
疲労評価の概要
シミュレーションで振動現象を可視化し、確認しながら効果的な改善対策を検討することができます。また、計測とシミュレーションを融合することにより、将来の寿命予測や故障予知を精度よく行うことも可能です。
詳しい説明資料は下記よりダウンロードください。
「シミュレーションを活用した設備・機器の疲労評価」資料ダウンロード
シミュレーションを活用した設備・機器の疲労評価の解説資料です。
疲労評価の流れや評価方法、評価のポイント、評価事例が掲載されています。
- 疲労破壊と疲労評価の流れ
- 疲労評価の方法① 応力による評価法
- 疲労評価の方法② ひずみによる評価法
- 疲労評価の方法③ 破壊力学による評価法
- 実働荷重の定義
- シミュレーションの手法
- 事例:翼固定リベット部の疲労強度評価
関連ページ
資料ダウンロード
さまざまな解析技術をまとめた資料をダウンロードいただけます。
解析技術の概要から、具体的な事例まで詳しくご紹介しています。ぜひ一度ご覧ください。